Roadmap to Building a Passive House
Passive House Construction: From Concept to Certification
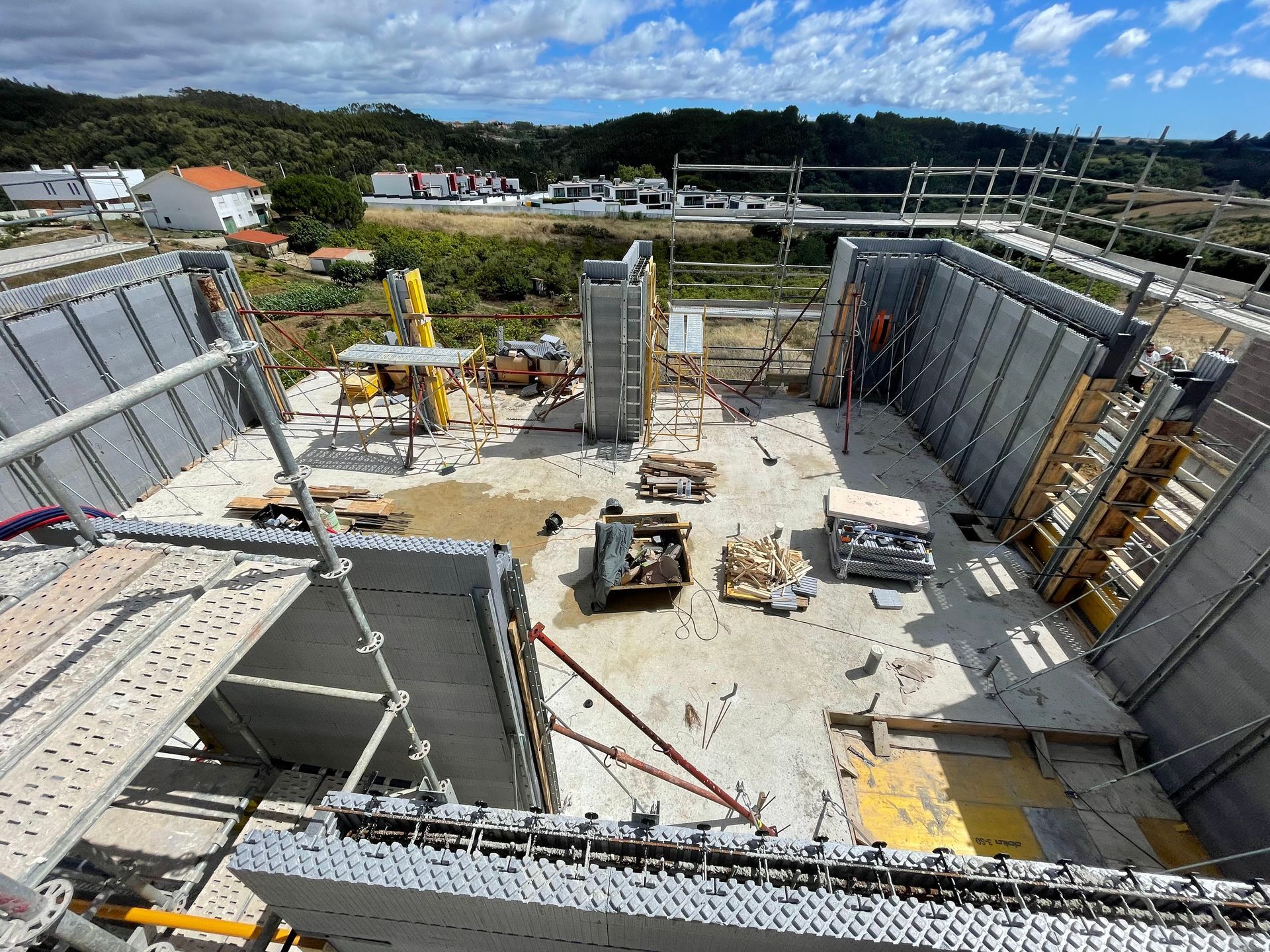
1. Passive House should be the goal from day one.
Even before the design phase, starting with the selection of the plot. South-facing orientations are favourable for our climate.
2. Establish a collaborative process between the client, the architect, and the Passive House Designer during the design phase, in order to align programmatic needs and functional aspects with the thermal and comfort benefits of the Passive House standard. A well-developed design stage allows for the integration of bioclimatic principles that contribute to strong performance.
3. A detailed execution project, bill of quantities, and technical specifications are essential.
They allow for early identification of construction challenges and help define the most cost-effective solutions.
4. Technical projects must be developed in accordance with Passive House principles.
The Passive House Designer/Architect must take an active role in coordinating all disciplines.
5. During the tendering phase, the technical specifications should clearly define the criteria guiding contractor proposals.
Alternative materials must meet the same performance requirements and, ideally, be Passive House certified. A+, A++ or eco-labelled products should only be accepted if accompanied by technical datasheets confirming performance.
6. Keep the PHPP (Passive House Planning Package) calculation tool updated at all times.
Changes during construction — due to stock issues, improved alternatives, or unforeseen costs — should be validated in the energy balance sheet.
7. Airtightness is a mandatory requirement for Passive House certification.
According to the standard, the blower door test can be performed either at the end of the build or once the airtight layer is complete.
Testing earlier allows for more efficient detection and correction of leaks. This procedure may require adjustments to the usual construction timeline and must be agreed with the contractor in advance.
8. Maintain focus and control throughout the construction phase.
Some Passive House criteria are not part of typical building practices. The Passive House Designer acts as the site inspector.
They must collect evidence on materials used: labels, thicknesses, installation procedures, datasheets, and technical catalogues.
9. Maintain a photographic and documentation archive of all relevant information.
10. Perform all final tests on equipment and systems at project completion.
Special attention should be given to the commissioning of the mechanical ventilation system in accordance with the Passive House standard.